Industrial Machinery
Industrial Machinery
Industrial machinery will
support manufacturing in Japan
also in the future.
support manufacturing in Japan
also in the future.
Industrial Machinery
Industrial machinery will support manufacturing in Japan also in the future.
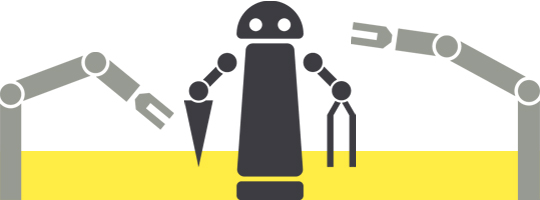
About Industrial Machinery Department
In the production site where labor-saving is increasingly accelerated, the introduction of robots is progressing rapidly.
In recent years, automation is progressing in various industrial fields. The production volume of industrial robots for automation is steadily increasing year by year, according to the market size estimates in Japan’s robot industry until 2035 that the Ministry of Economy, Trade and Industry announced, it is estimated that the domestic market alone will balloon to 9.708 trillion yen. 50% of them are robots that are used in the service sector, the next largest group is the 25% of the industrial robots. In the future, decrease in the labor force is expected in Japan. Therefore, along with the labor-saving at manufacturing sites and the promotion of automation, it is inevitable that the introduction of industrial robots continues to increase. Eto is committed to industrial robots, which forms the core of the future growth strategy of Japan.
Japan’s robot industry market size estimates
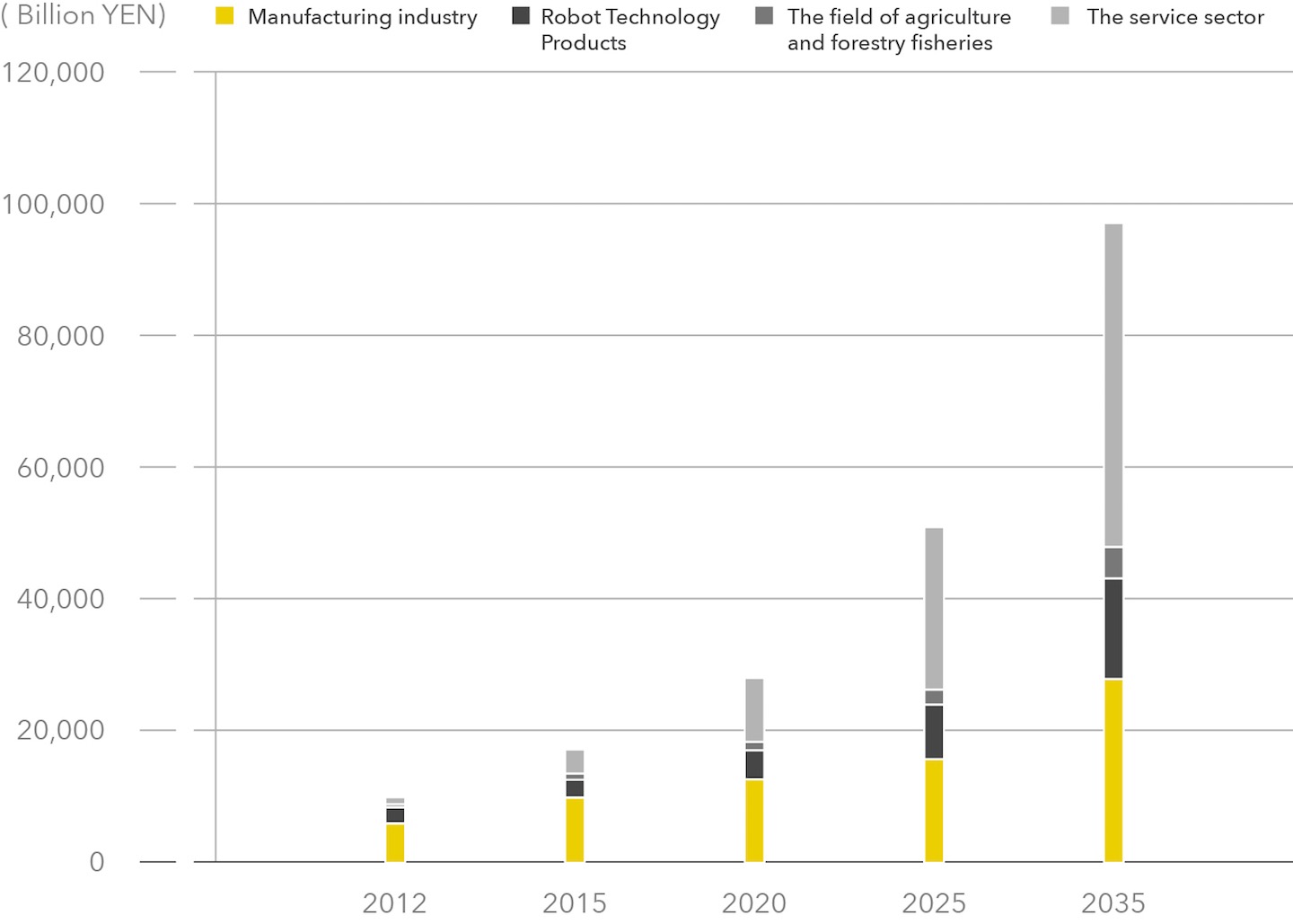
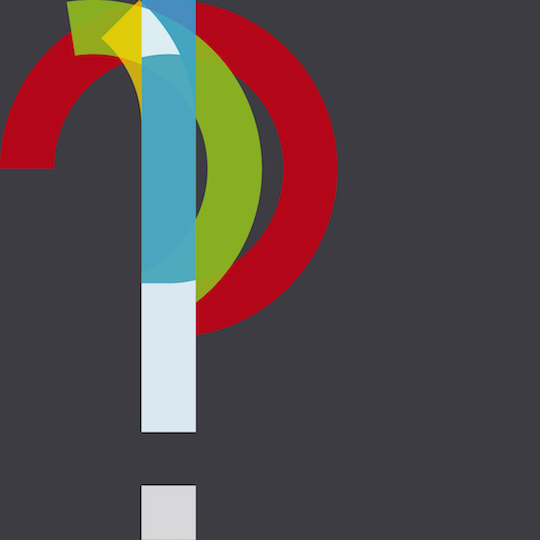
Case Study : Improvement of the mass-production line of industrial robots
Aiming at automated assembly operation, thereby shortening the process significantly.
“Automation does not mean that machines take away the work of man, it is rather intended for man to concentrate on the work that requires higher productivity.”
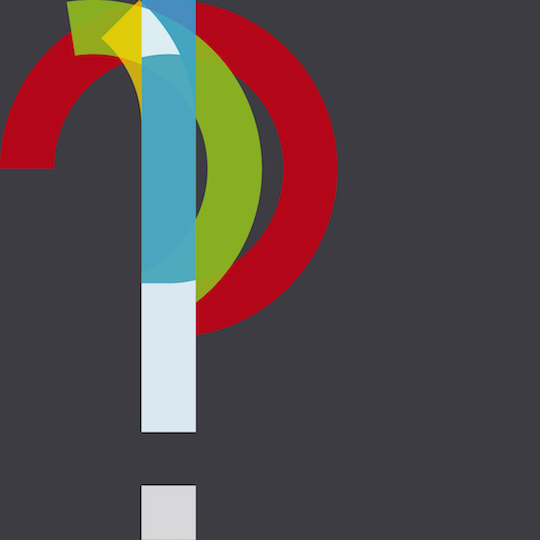
Case Study
Improvement of the mass-production line of industrial robots
Improvement of the mass-production line of industrial robots
Aiming at automated assembly operation, thereby shortening the process significantly.
“Automation does not mean that machines take away the work of man, it is rather intended for man to concentrate on the work that requires higher productivity.”
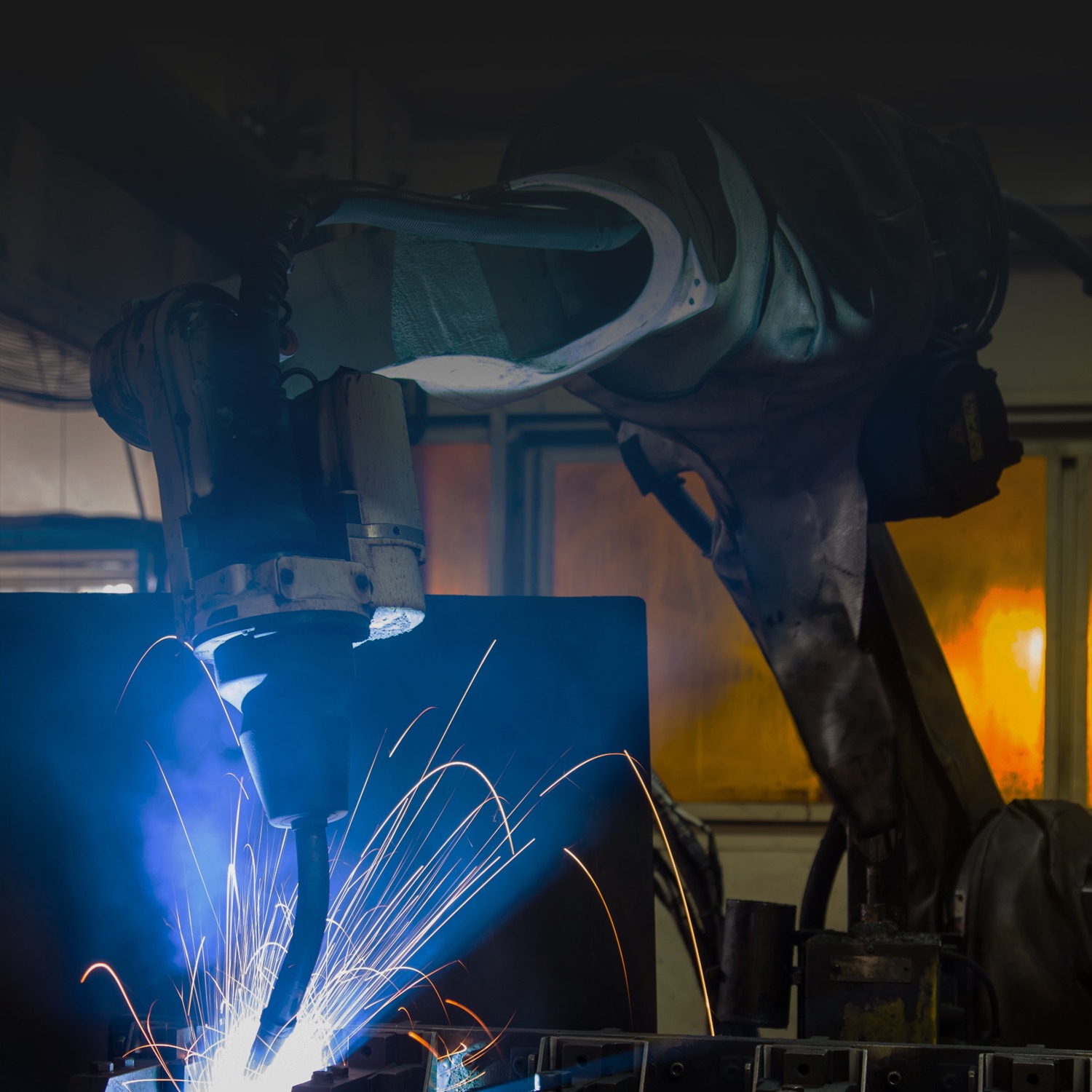
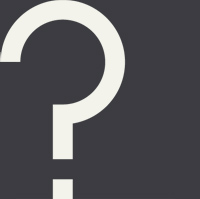
Client’s Problem
Delay of production due to the production volume surge and limitations of the human work.
The client was concerned that because the incorporation and assembly were manually carried out by workers in the manufacturing site, they might not be able to follow the production plan due to the further increase of the production volume in the future. For this reason, they were in such a state in which the delay of production was compensated by promoting efficiency and supporting work of automatic incorporation by robots. However, for the large products that are built with a large number of components like industrial robots, the increased number of parts will significantly increase the amount of work in embedding, and the burden on the workers will approach its limits. As a result, the built-in defects from fatigue and the oil stains on the floor from dropped parts, etc. occur, leading to degradation of quality and deterioration of the work environment. There are limits to the improvement of productivity and efficiency of workers. Eto thought that there was a need to review the entire production.
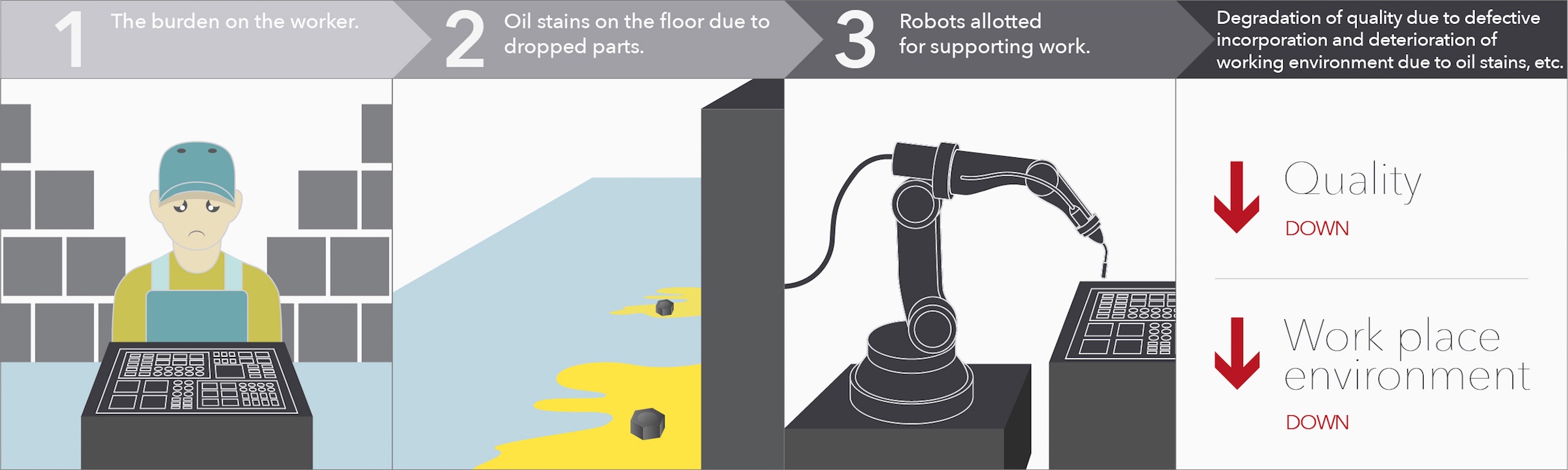
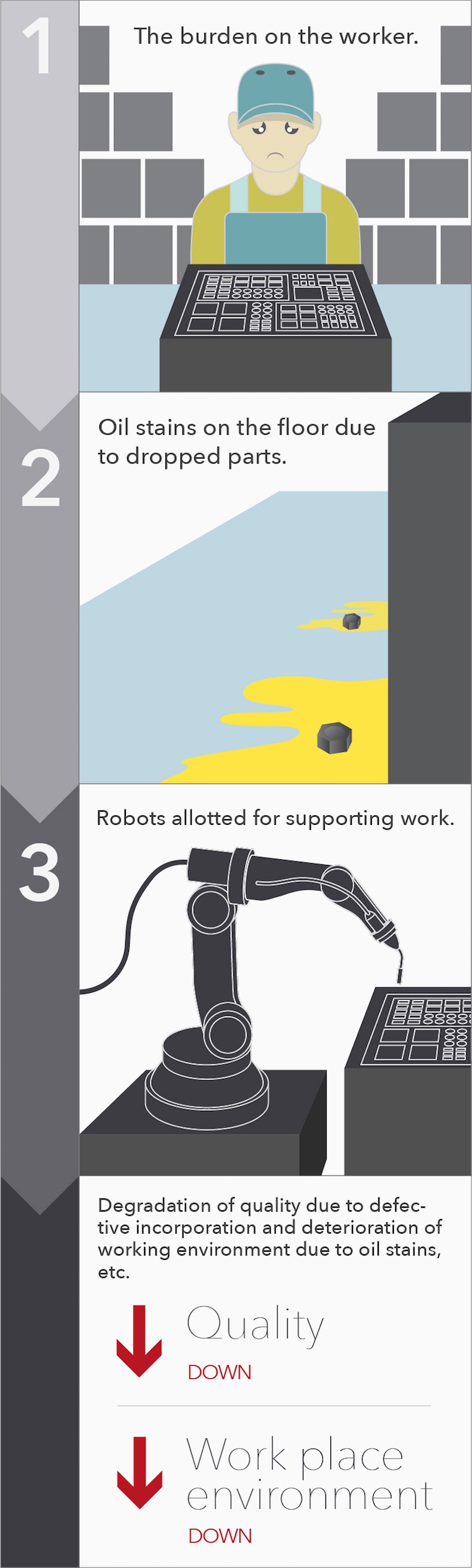
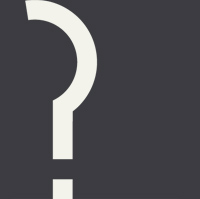
Proposal
Leading to the optimal solution by considering the collaborative process of parts incorporation.
In response to the limitations of the built-in work by hand, Eto reviewed the mass-production line and began to study the places where improvement is possible. Specifically, it was to find parts with problems in the built-in work and to improve the parts, including the collaborative process in which the parts are incorporated. Although the effect of the change of a part unit is small, the outcome of the improvement of the mass-production line by the process change is tremendous. We will specifically introduce Eto’s proposal.
Finding problems in the mass production line
Eto focused on the built-in work of the disc spring.
In considering the issues of the mass-production process, we focused on the disc spring that is built by hand. In the assembly process of the robot arm, in the past, workers incorporated the “disc spring” into the hexagon socket head cap bolt, but there is a possibility that a defective product occurs when the bolt is fastened without a “disc spring” being securely incorporated due to the fatigue and mistakes of workers. So we have decided to consider improvement measures, focusing on this “disc spring.”
Incorporation of the disc spring
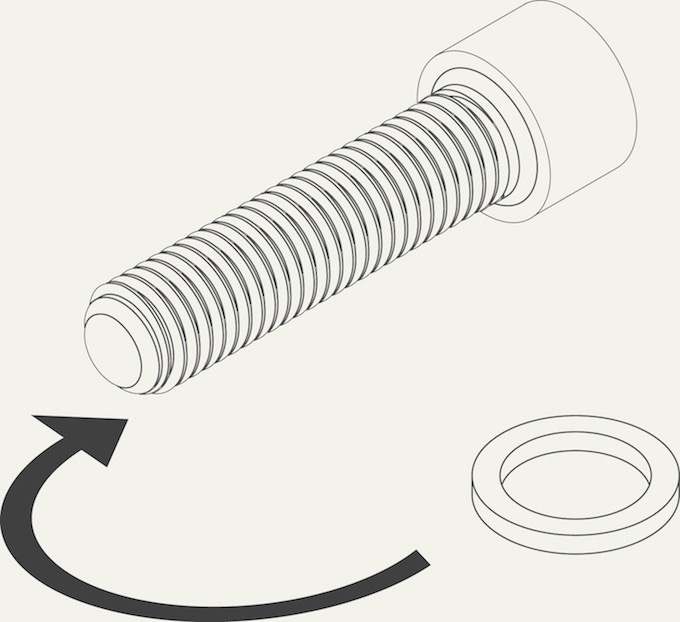
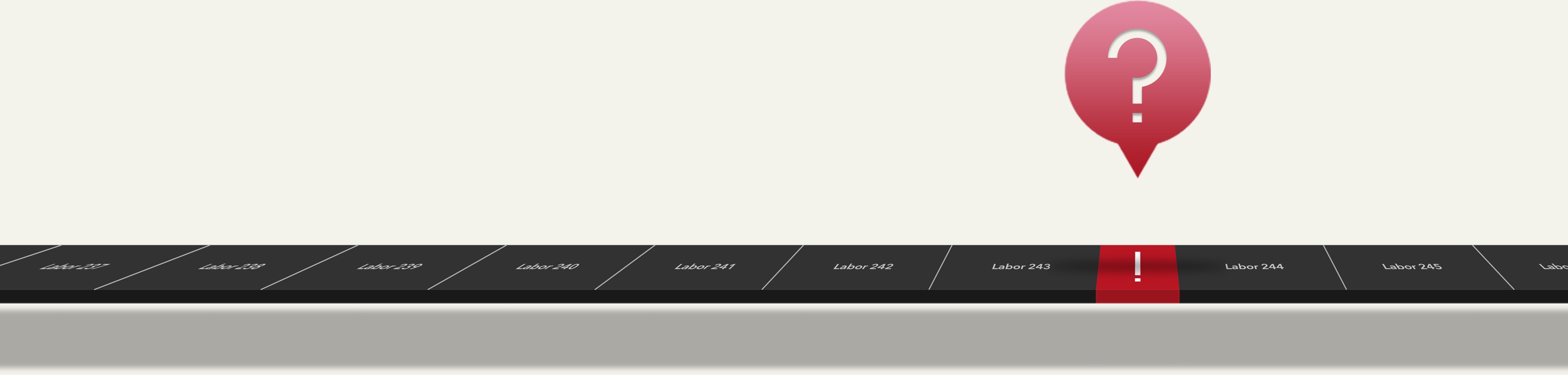
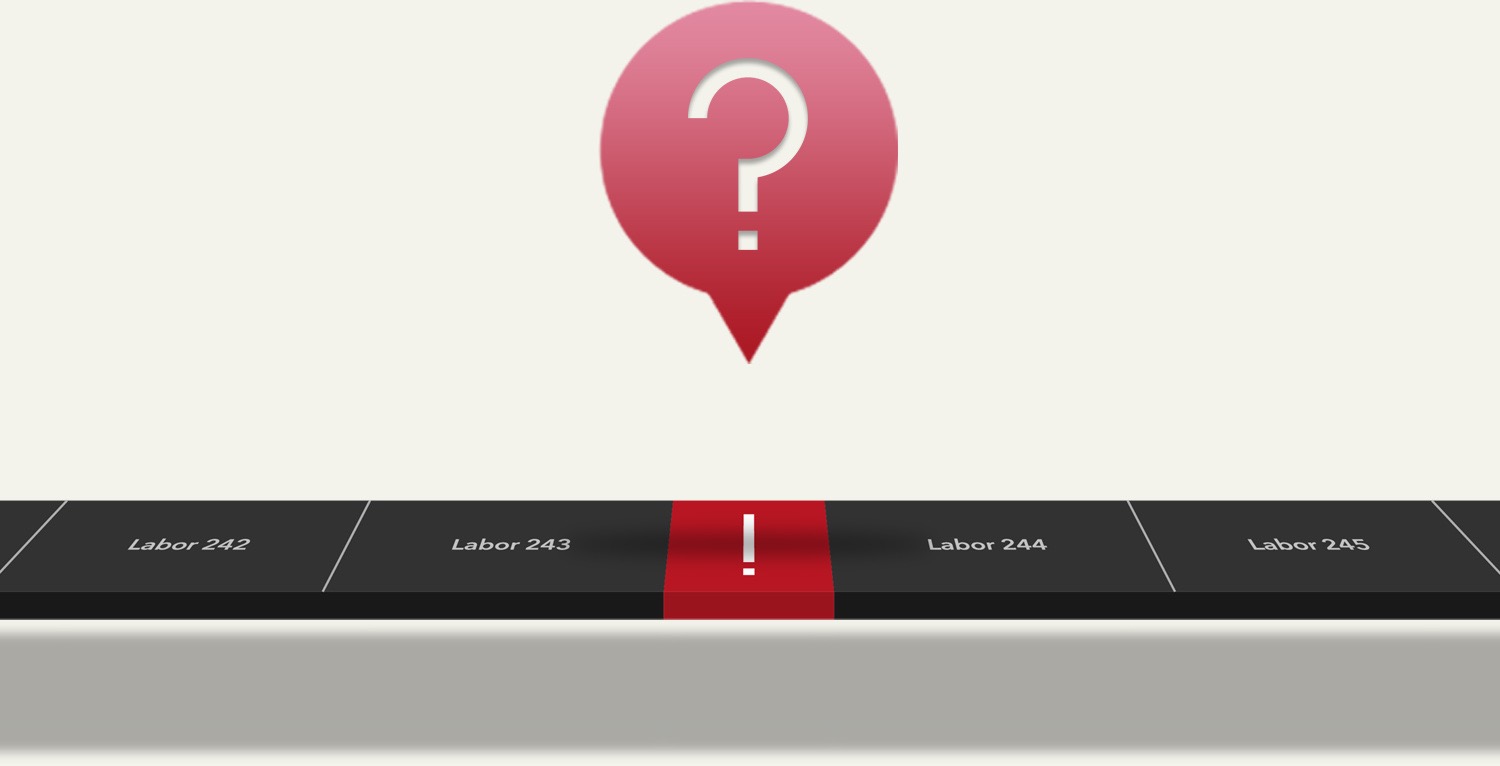
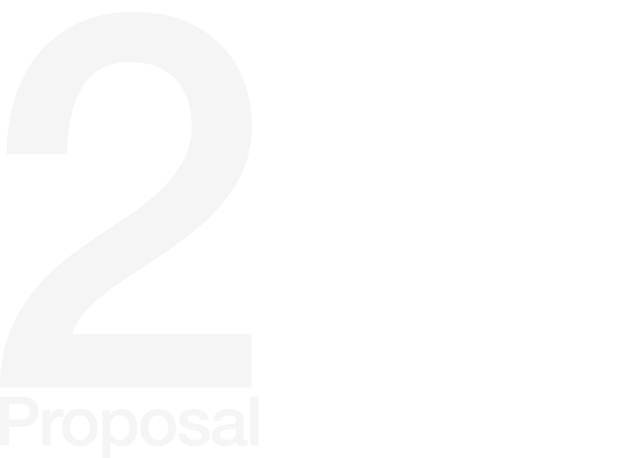
Improvement method that takes into account the front and back of the disc spring parts
We do not intend to present the replacement of parts. Re-building the production activities is important.
Focusing on the disc spring, we aimed at improving the entire mass-production line. Eto considered whether this built-in work itself could be reviewed. And, what Eto proposed was to integrate the disc spring into a part. If the part can be switched to an integrated part, the built-in work of the spring is no longer needed, you can prevent the defective incorporation. In addition, the deterioration of the working environment due to the spring falling will be avoided. And, more than anything else, valuable human resources and robots that have been pressed for time by the supporting work so far can be allotted to the work that requires higher productivity. It is a great value to be able to contribute to the improvement of the entire production process, including the working environment, by eliminating one part.
Integrated disc spring
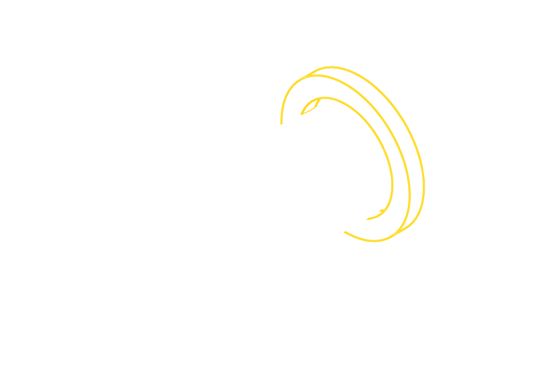
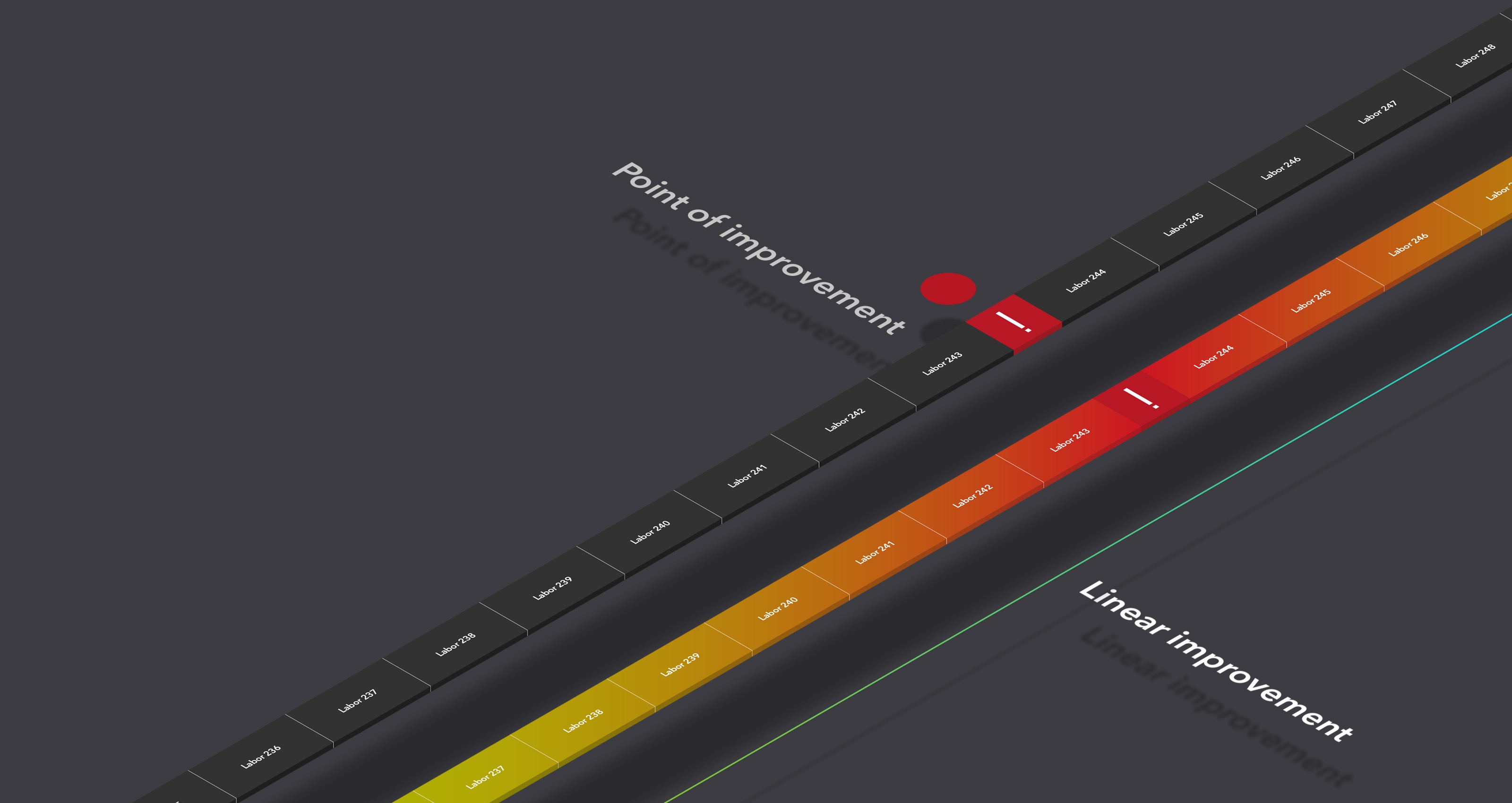
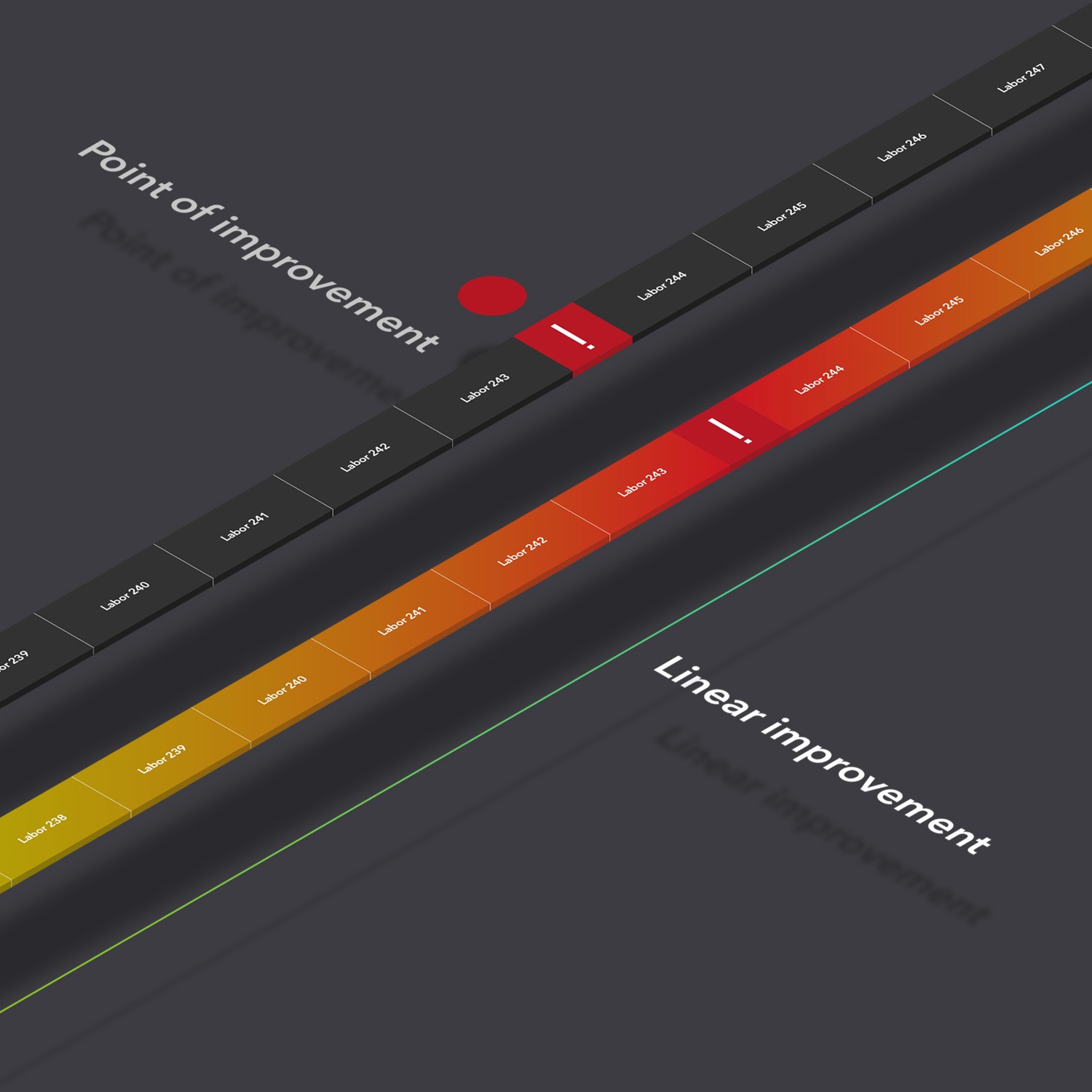
Not proposing only a solution to a problem, we find a problem and at the same time present a solution.
The piece price of the hexagon socket head cap bolt with a disc spring integrated is increased, but the total use number exceeds 30,000 pieces and the total man-hours are reduced, so from the viewpoint of the total cost a significant cost reduction was expected. In addition, when considering that improvement of the work environment of the global service centers that this robot manufacturer deploys is simultaneously made possible, substantial advancement and great results could be expected from this solution. Not proposing only a solution to a problem, Eto sometimes finds a problem and at the same time presents a solution.
The total use number of the hexagon socket head bolts
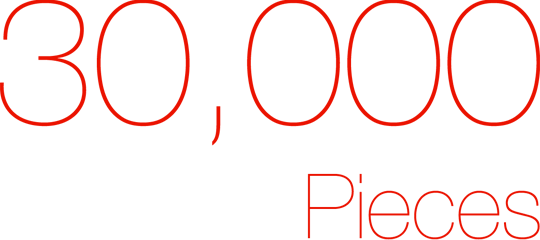
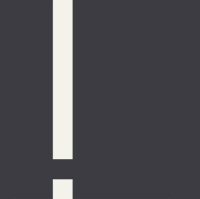
Results of proposed
Shortened work time and a significant cost reduction were achieved.
Results of the verification test showed that by the proposed method of Eto, fastening work man-hours at the mass-production process and maintenance work were greatly reduced. In addition, although the piece price of the bolt increased, a significant cost reduction was achieved when including personnel expenses of workers who were no longer needed. We will introduce the achievements.
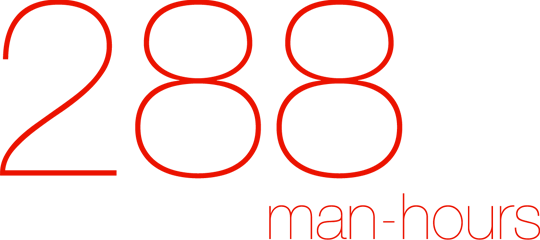
Reduction number of man-hours
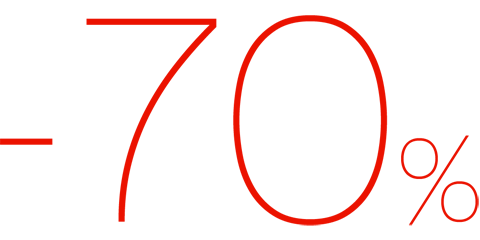
Percentage of total cost cut
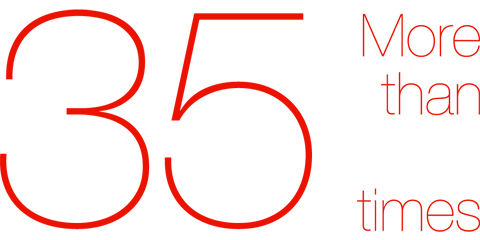
Investment efficiency
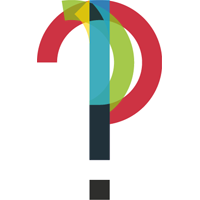
Summary
To explore the issues thatmust be solved.
There is sometimes a case where the nature of the problem is hard to ascertain only through solving the problem of the part unit. Therefore, it is necessary to solve a problem through an approach that looks down the entire mass-production line. In the case study, we showed an example of the “disc spring.” Aiming at achieving two goals of the efficiency of production and the environmental improvement for the working people at the same time, Eto actively implements the evolution toward robots with greater diversity and the investigation and review of the mass-production line, and is continuing to discover the place where improvement is possible and to propose the solutions.
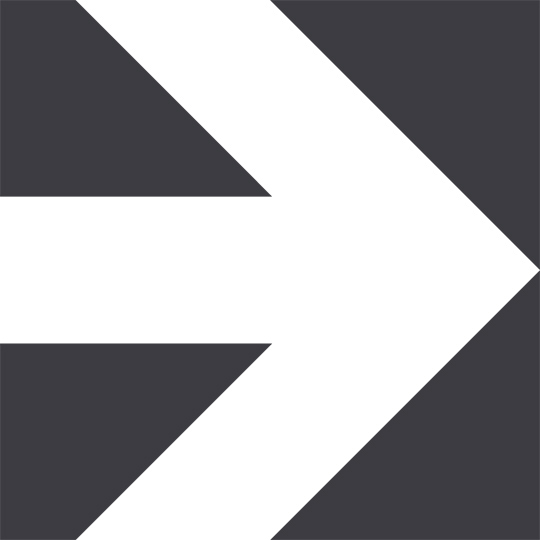